In the orbital welding process, a welding tool is rotated 360 degrees (or 180 degrees in double up welding) around a static workpiece.
When to use Orbital Welding
When manual welding is used in specific positions, such as down-hand and overhead, it can be challenging to establish high standards of safety and quality.
Due to the user's limited access, it can be difficult for the welder to regulate the weld pool while balancing surface tension and gravity force in various torch positions, which can result in poor welds.
This problem can be resolved by automatic orbital welding technology, albeit a welder will still be needed to oversee and monitor and adjust the operation.
Since the manufacture of tubing results in creating consistent outside diameters that are better for a proper fit up in the weld head.So orbital welding technology is more frequently used on tubing than on pipes.
Even with unique materials, pieces with a considerable wall thickness, small diameters, or hazardous conditions, orbital welding may produce highly repeatable, reliable welds. These elements collectively have led to the widespread adoption of orbital welding technology across numerous sectors and applications.
While the cost of the necessary equipment is somewhat costly (5–10 times as much as conventional equipment), orbital welding can provide 2-3 times higher productivity than traditional TIG welding.
When to use Orbital Welding
When manual welding is used in specific positions, such as down-hand and overhead, it can be challenging to establish high standards of safety and quality.
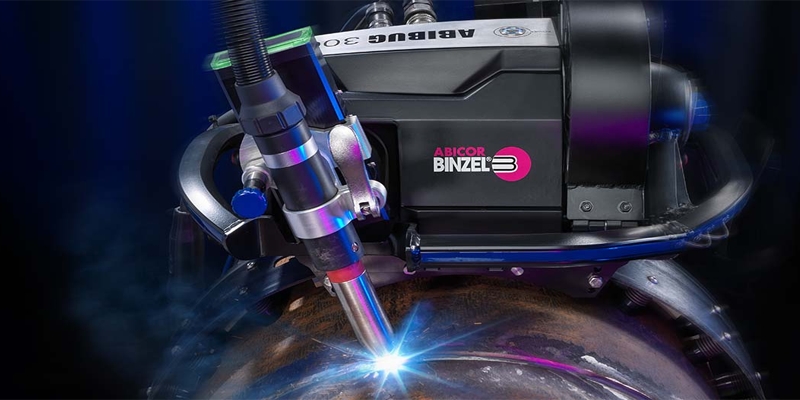
Due to the user's limited access, it can be difficult for the welder to regulate the weld pool while balancing surface tension and gravity force in various torch positions, which can result in poor welds.
This problem can be resolved by automatic orbital welding technology, albeit a welder will still be needed to oversee and monitor and adjust the operation.
Since the manufacture of tubing results in creating consistent outside diameters that are better for a proper fit up in the weld head.So orbital welding technology is more frequently used on tubing than on pipes.
Even with unique materials, pieces with a considerable wall thickness, small diameters, or hazardous conditions, orbital welding may produce highly repeatable, reliable welds. These elements collectively have led to the widespread adoption of orbital welding technology across numerous sectors and applications.
While the cost of the necessary equipment is somewhat costly (5–10 times as much as conventional equipment), orbital welding can provide 2-3 times higher productivity than traditional TIG welding.